PCBs (polychlorinated biphenyls) in oil and transformers
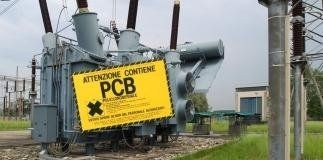
The generic term PCB(polychlorinated biphenyl) refers to a family of 209 chemical compounds, called congeners. The first laboratory synthesis of PCB dates back to 1867, but global production only started in 1929 and lasted until the mid-1980s, when the first laws were passed to restrict use of PCBs because they represented a serious danger for humans and the environment.
PCBs have been marketed in the form of mixtures formed from a complex mix of congeners to which chlorinated solvents have been added, identified by various commercial acronyms such as Aroclor, Askarel and Apirolio.
Compared with mineral oils, synthetic fluids based on PCB and PCT (Askarel) as insulators/coolants for transformers offer the following advantages:
- greater chemical resistance,
- better dielectric characteristics,
- low viscosity and
- greater fire resistance.
It has long been known that in the event of thermal oxidation and at uncontrolled temperatures around 500 °C, PCBs can form products that are highly toxic for humans and the environment, such as polychlorinated dibenzodioxins (PCDDs) and polychlorinated dibenzofurans (PCDFs).
Sea Marconi and the battle against PCBs
The story of Sea Marconi began in 1968 and is characterised by events and important discoveries in the field of PCBs (polychlorinated biphenyls) and dioxins.
In this context, Sea Marconi has been at the forefront of designing pioneering solutions worldwide and contributing to the drafting of standards and laws (national and international) for the sector.
The Sea Marconi experience
1979
With CODEC-PCB, Sea Marconi provides a service for inventory, controlled possession, management and decontamination of equipment with PCB.
1982
First patent for the CDP Process ® for the decontamination of equipment through dehalogenation/detoxification of PCBs, PCDD-dioxins and PCDF-furans.
1983
First in the world to successfully validate, through experimentation, the dehalogenation and detoxification of the most dangerous dioxin known, the so-called Seveso dioxin (2,3,7,8-TCDD tetrachlorodibenzodioxin).
1984
Starting from 1984, the CDP Process® has been improved with further international patents and applied in over 50 countries.
2007
The CDP Process ® is classified by the Ministry of Environment (Min. Decree 29/01/2007) as Best Available Technology for the decontamination of equipment with PCBs, in particular of transformers contaminated by PCBs in service even under load.
TODAY
The CDP Process ®
is classified as BAT(Best Available Technology)/BEP (Best Environmental Practice) in international UNIDO projects, funded by the GEF, to support developing countries in achieving the objectives of the Stockholm Convention.
These countries include, for example, Mongolia and Macedonia, for which Sea Marconi has supplied an advanced plant for the decontamination of oil contaminated with PCBs.
With the same principles, Sea Marconi has developed the “ PCB-Free Programme ”, which is being applied in Africa, Asia, and Central and South America. It is an integrated solution (inventory services, control and monitoring with analyses and diagnoses; decontamination procedures and technologies) finalised towards the life cycle management (LCM) and decontamination of transformers and oils with PCBs.
In the battle against dioxin and PCBs, Sea Marconi can be defined in its own right as an example of excellence in innovation, taking its "sustainable solutions" from Italy to the rest of the world.
At the last international conference in Geneva(May 2013), there was talk of 2028 as the target year for the complete decontamination of PCBs worldwide; nevertheless, the regulatory scenario in the world is extremely diverse: in Italy and Europe the limit for PCBs is 50 mg/kg(even if the threshold of 25 mg/kg is a shield against possible temporary deposits, transfer of oils or future revisions of the standard), but in some countries the limit has been reduced to 2 mg/kg. Then there are cases such as Japan where the legal limit for PCB is 0.5 mg/kg.
It should be noted that current legislation ( Directive 96/59/EC - Legislative Decree 209/99 Art. 5, paragraph 2 - Guide CEI 10-38, Chap. 8.2) requires the following
Decontamination obligations
equipment volume | PCB concentration (mg/kg) | expiry |
---|---|---|
< 5 dm3d> | > 50 | 31 December 2005 |
< 5 dm3d> | between 50 and 500 | end of service life |
< 5 dm3d> | > 500 | 31 December 2010 |
Today, from a regulatory standpoint, no transformers should be contaminated above 500 mg/kg.
Again, in theory, all transformers containing PCBs that can still be used (because they are contaminated between 50 and 500 mg/kg and in g ood functional state) should be listed in the national inventory.
CAUTION: “In good functional state".
Legislative Decree 209/99, Art. 5, paragraph 4
“ Transformers (contaminated between 50 and 500 mg/kg) may be used pending decontamination or disposed only if in good functional state, with no leaking of fluids and the PCBs that they contain compliant with the standards or technical specifications related to dielectric quality
”
. Therefore, utmost attention must be paid above all to:
- the frequency of diagnostic checks of the dielectric fluid;
- the parameters being checked;
- the evolution of these parameters over time;
- the inspection conditions of the transformer;
- the value of PCBs measured (date, methodologies used and the accuracy of this value)